The Popularity of ERP Systems in the Manufacturing Sector
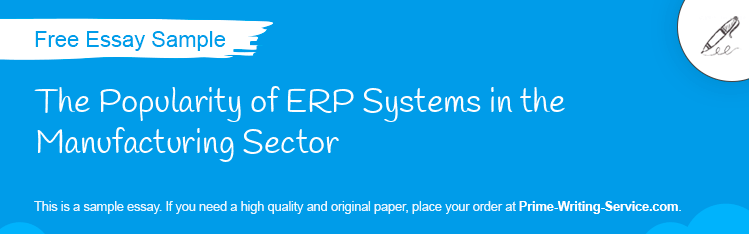
Introduction
Enterprise Resource Planning (ERP) refers to enterprise-based software or systems that integrate the key functional areas of an organization. In other words, ERPs are information systems that carry out business and financial planning functions, which might previously be handled by generic standalone applications. Some of EPR fundamental modules include supply chain management (manufacturing, distribution, and purchasing), financials, sales orders processing, and human resources. This software has become pivotal strategic tool or system in today’s globalised business environment. ERPs were first deployed in 1990s to address issues such as increased regulation and the Y2K transition (Gupta 2013). They are traced to the manufacturing industry, where generic versions of the application were used for Manufacturing Resource Planning (MRP). Since markets globalised and new technologies emerged, manufacturers markets experienced a dramatic reduction in margins alongside with increasing customer expectations. In response to these developments, more functionality was added to MRP. Moreover, the business transformation into the manufacturing industry contributed to ERP development. This paper explores the popularity of these systems in the manufacturing industry, as well as specifies their benefits. In addition, challenges manufacturing firms face while implementing ERPs are also discussed. Finally, recommendation for future research is presented.
Calculate the cost of essay
Enterprise Resource Planning (ERP) Systems
Essentially, an ERP is a suite of integrated software modules that manage the core resources of a business. In other words, it coordinates and manages enterprise processes and resources (Gupta 2013). For instance, when a manufacturer sells a product over the Internet, data is sent to the various department including customer relations, manufacturing, finance, and supply chain management. ERPs are developed in-house or procured as standard application packages. In the current business environment, most clients prefer a hybrid of in-house and on-shelf systems to systems developed in-house. According to Gupta (2013), stand application packages are designed and developed by vendors to meet the basics business requirements for the public. On the contrary, ERPs developed in-house are software suites, often developed from scratch for a specific enterprise.
ERP is an industry-driven term and concept for a set of processes and activities supported by software with multiple modules, which helps manufacturers or other business entities to manage their core business function. Typically, it uses various components of computer hardware and software to facilitate integration. Enterprise systems have a centralized database of storage area networks that archives all data from all the software modules. Some of the leading global ERP vendors include Oracle e-Business Suite, SAP Business One, SAGE, Microsoft Dynamics, Lawson Software, and NetERP from NetSuite (Gupta 2013).
Comparison between MRP, MRP II, and ERP
Manufacturing Resource Planning (MRP II) is an information system designed to integrate all manufacturing and linked applications, including material requirements planning (MRP), decision support, distribution, and accounting (Salimi, Dankbaar & Davidrajuh 2006). MRP entails ensuring that materials are available for manufacturing a specific product in a specific volume. MRP II handles the job aspects such as tracking inventory, ordering, and ensuring capacity. Enterprise systems serve all functional departments in company (Gupta 2013). In essence, ERP system enables integration and coordination of departmental activities. Understandably, its concept evolved from MRP II, which in its turn evolved from the rationale of MRP. The main function of this system is to guarantee that material availability (Salimi, Dankbaar & Davidrajuh 2006). In other words, MRP II is used to procure resources for both internal purposes, as well as for product sales and distribution.
Limited time offer
Benefits of ERP
In 2013, the global ERP market grew by 3.8 %, which was a considerable growth compared to the 2.2 % growth in 2012 (Columbus 2014). This implies that ERPs are gaining popularity, probably due to their numerous advantages. Enterprise Resource Planning software increases information flow within a firm. It also automates the business process, thus increasing productivity at lower cost, and with fewer errors. Contemporary ERP software is more flexible, hence allowing the enterprise to develop workflows with ease (Gupta 2013). Integrated ERP system in manufacturing firms improves supply chain performance in various business units. The centralized storage area network (SAN) improves data security, availability, and integrity (Auramo, Kauremaa & Tanskanen 2005). It follows that data can be accessed faster than in legacy systems. By using the lean management tools of Kanban, Just-in-Time (JIT) and VMI, manufacturing firms will be able to reduce their expenses significantly (Womack & Jones 2005).
Lean Aspects of ERP
The aim of implementing an ERP system in a manufacturing firm is to increase quality, productivity, profit, market share, and customer satisfaction. Furthermore, ERP is intended to reduce costs of production and the prices of the manufactured products without compromising quality. The manufacturing module of an ERP consists of several processing units including technical projects, scheduling, engineering, workflow management, manufacturing process, automated flow and quality control (Berry, Whybark & Jacobs 2005). ERPs have a significant impact on manufacturing firms. They integrate an entity’s data, providing a centralized source for the entire firm to share data and information typified with high integrity and accuracy. The efficiency provided by these systems is registered from the elimination of redundancy. In other words, information is entered only once. Moreover, it provides various functionalities, including manufacturing planning, advanced planning systems, and control systems (Berry, Whybark & Jacobs 2005; Villegas & Smith 2006). Previous ERP system has done little to achieve high efficiency on plant floors. Some of the problems with earlier ERP systems include inefficient workflows, complex bills of materials, and unnecessary data collection. Changing from plant-floor management in enterprise systems to lean (demand-pull) ones was meant to overcome some of these hurdles (Wacker & Sheu 2006).
Benefit from Our Service: Save 25%
Along with the first order offer - 15% discount, you save extra 10% since we provide 300 words/page instead of 275 words/page
There are several differences between lean manufacturing and ERP. One of the main differences is that ERP stresses on plans based on sales projections. On the other hand, lean manufacturing links productions to actual customer orders (Womack & Jones 2005). Enterprise systems track material price and activities, which generates non-value-added transactions. On the contrary, lean production emphasizes on speed and seamless production. This gap has been eliminated by removing ERP reports and logs that entail push motivation instead of pull one. Other manufacturers prefer changing ERP software. Contemporary vendors have included lean features in their software. Some of the lean manufacturing features that have been included in ERPs include exception reporting, mathematical models, and simulation to synchronize production with demand, demand smoothing and Kanban replenishment calculation (Womack & Jones 2005).
Lean ERP systems have been essential while improving efficiency within manufacturing firms in response to the volatile global economic landscape. Lean approaches are useful for levelling upstream production. On the other hand, agile approaches centre on ensuring the ability to respond to the ever-growing customer expectations. These methods have also been useful in service industries. Essentially, lean concepts focus on the internal environment of an entity in a high-quality approach and optimize human capital. Lean ERP systems are pivotal while enabling manufacturing firms to not only survive, but also to thrive in the global markets. The critical enabling tool in such systems is an information technology. ERP supply chain systems serve as global linkages to suppliers and customers, thereby, supporting collaboration. Furthermore, they provide more opportunities for supporting the implementation of lean concepts.
VIP Services
$2.00Extended revision period
$3.00SMS notification of the order status
$3.66Get order proofread by editor
$4.40Get order prepared by top 30 writers
$5.99Get a full PDF plagiarism report
$9.99Get VIP support
20% OFFVIP services package $23.23
Aspects of ERP Supply Chain Management Systems
A supply chain or logistic network is a coordinated system of people, business processes, organizations, resources, and information involved in the process of moving a product from supplier to end user. Typically, supply network consist of sales channels, service providers, consumers, distributor, and manufacturers (Monczka et al. 2011). Supply chain activities transform components and raw materials into finished products that are delivered to end customers. The supply chain management (SCM) module contains several units, such as supply chain, purchasing, inventory, supplier scheduling, claim processing order entry, inspection of goods, and commission calculation.
One of the key factors of enterprise system implementation by manufacturing entities is to improve communication and interactions with customers and suppliers. Therefore, ERP is designed to support supply chain activities. There are numerous benefits to be gained because from ERP supply chain systems installing. Manufacturing firms implementing open systems stand to obtain more advantages in logistic and ordering operations. Moreover, the Internet provides a valuable information communication infrastructure for sharing knowledge and negotiation (Kelle & Akbulut 2005). In fact, transaction processing becomes significantly faster and easier than in conventional supply chain systems. Following these observations, manufacturing companies can be propelled by more competitive and efficient cloud-based supply chain units.
According to Caruso (2010), ERP system improves supply chain performance by developing superior customer interaction and insight. Manufacturing firms need to build long-lasting relationships with their customers by listening to and understanding them. Such a broad perspective can be obtained from various data sources, primarily supply chain systems. Other valuable sources include field services systems; customer service; internal database, sales and marketing, and the intelligence gathered from informal interaction with customers. Such an integrated perspective is provided by ERP systems, which enable manufacturing firms to gain a better understanding of their customers’ needs and expectations. Consequently, an entity can differentiate its offerings leading to a competitive advantage or increased profits.
Try our Top 30 Writers
Benefit from the incredible opportunity
at a very reasonable price
Order only for $4.40
ERP systems also enable manufacturing firms to increase their global visibility within competitive or demand-propelled supply chain (Caruso 2010). In the current era of tight cost management, manufacturers have to optimize their inventory investments while providing superior customer service. To achieve this, it is needed for them to have a thorough understanding of their inventory throughout the product life cycle. An enterprise system can provide such valuable information. Being informed on where and when stock in needed helps manufacturers to create effective production and re-supply plans in critical customer relationships. Beyond archiving the right data and information for internal operations, manufacturing entities must also be in a position to provide visibility into product availability and inventory to entities in the external environment. In a demand-driven manufacturing atmosphere, real-time intelligence is required to make effective and timely decisions. It implies that supply networks should be open to new technologies, including barcoding and radio–frequency identification (RFID) to support tracking and any regulatory compliance requirements (Caruso 2010). ERP systems can enable manufacturers to meet their needs in such areas.
As noted by Caruso (2010), integrated ERP software can improve supply network performance through global sourcing, supplier, integration, and lean management. In the manufacturing sector, managing the lower cost is essential. It follows that lean manufacturing principles should be applied. Furthermore, the manufacturers should connect their operations to the best suppliers on the global landscape. Locating such suppliers’ calls for a comprehensive database, which would enable a manufacturer to determine new opportunities at a lower cost, as in the case of supplier in new markets (Auramo, Kauremaa & Tanskanen 2005). Consequently, manufacturing firms must have real-time and reliable connection to suppliers in order to respond to demand and production data, such as critical engineering modification and new product designs. Contemporary ERP systems include the capabilities and process that help users ensure lean operation.
Try our VIP Support
Benefit from the incredible opportunity
at a very reasonable price
Order only for $9.99
Challenges of Implementing ERP in a Manufacturing Firm
Despite the widespread adoption of ERP systems in the manufacturing industry, manufacturing firms faces several hurdles during these systems adoption. Challenges emerge from both the internal and external environments of manufacturing firms. Like any other technology, ERP systems come with pitfalls or challenges. Observably, unless all the entities in a supply network can use the same ERP systems, enterprise systems can become barriers to communication (Gottfredson & Aspinall 2005). It follows that, units with a supply chain are likely to benefit more by adopting ERP from a single vendor. This could be economical in the long term. However, it imposes high costs on vendors if they are forced to spend on a system in order to maintain business contact with a client. The main part of the communication problems across enterprise systems is linked to variation in software tools and data incompatibility.
Part of the challenges is related to system openness. Ideally, supply chains need open systems, but most of them were designed and developed on the rationale that relatively a few people would need to access the archived information. This resulted in a pricing mechanism where license fees for single users were very expensive. Complex ERP systems can be difficult to customize (Gottfredson & Aspinall 2005). Since business processes are regularly re-engineered to adapt new ERP systems, problems with staff and processes emerge. In addition, ERP systems implementation may be very costly for manufacturing firms. However, this challenge has led to the emergence of simple ERP software for medium-sized enterprises.
Affiliate Program (Earn 10%)
Earn 10% from all orders made by people you bring!
Your people also get 17% discount for their first order
Start earnings now!
Typically, ERP implementations can impose restrictions on communication with suppliers and customers. In fact, ERP systems that focus on the internal environment can limit supply chain coordination. As a matter of fact, enterprise systems provide meaningful integration over supply chains in the long run. However, in short durations, ERP systems could constrain logistical operations. The other challenge is the inherent trade-off between system openness and control. The existing ERP systems still need greater openness to support activities integration between customers and suppliers across the entire supply chain. Vendors should collaborate to increase support for cloud or web-based operations. In other words, there is a pressing need for an application programming interface (APIs) to improve openness or data compatibility. Ideally, an ERP system should support customization by availing standard interfaces.
Recommendation for Future Research
In the contemporary business landscape, manufacturers are required to synchronize with technological advancements occurring rapidly. As trendy concepts such as Bring Your Device (BYOD) continue to make a significant impact, it is imperative that an IT department in the manufacturing sector embraces innovative technologies. ERP, in particular, stands to benefit from adopting a flexible strategy or approach to innovations (Gottfredson & Aspinall 2005; Guan et al. 2006). As technological innovations continue to increase in a flash, it is imperative that information technology embrace new trends and technologies in the same pace. In this case, it is obvious that ERP stands to gain a lot in synchrony. According to Mathews (2014), some of the trends that are projected to shape the future of ERP include big data analytics, Internet of Things (IoT), and wearable technology. It follows that these areas are worth researching.
Choose your discount
Internet of Things is an innovative concept in which objects, including electrical appliances and car are capable of transferring data of communication networks without human input (Matthews 2014). In reference to ERP, devices can be attached to manufacturing systems or sensors feeding web-based applications. Information, such as performance and status, can be easily accessed and analysed. So, it enables manufacturing entities to identify issues like underutilized assets, or areas that need maintenance. Furthermore, service engineers could receive asset data and job instruction automatically as soon as they flagged for repairs. Manufacturers have become dependent on ICTs and, consequentially, they have accumulated a vast amount of raw data that has been archived and underutilized (Auramo, Kauremaa & Tanskanen 2005). As employees continue to connect to the Internet and IOT connects to manufacturing tools, data generation is projected to grow exponentially. Therefore, data mining and warehousing, as well as other analytical tools can be used by manufacturers to make precise predictions and patterns that form an informed approach to strategic management.
The wearable technology was one of the focal points at the 2014 Consumer Electronics Show (CES). In the same context, Gartner projected that the technology market for wearable devices will be worth $10 billion by 2016. Given the fact that there is a host of the above mentioned technology applications in the manufacturing workplace, it is worth researching in reference to its relationship or impact on ERPs. For example, smart watches depict progress compared to smartphones and PDAs because they are easily accessible and much less likely to be dropped or misplaced. Wearable devices designed to monitor environmental factors such as heat, UV exposure, and air pollution can help manufacturers improve the management of safety and employee health (Matthews 2014). Over the next decade, technologies like big data analytics, the IoT, and wearable stand to reinvent business process across the manufacturing sector. Therefore, taking an innovative approach to the new technologies adoption, manufacturers stand to increase productivity, save time, and minimize costs, outcomes that will be mirrored in the bottom-line of manufacturers that embrace new technologies (Gottfredson & Aspinall 2005).
Plagiarism check
Attractive plagiarism check option: ensure
your papers are authentic!
Conclusion
ERP is an enterprise-based information system that controls and combines all the core enterprise functions or processes. It is designed to integrate and optimize business transaction and process within an enterprise. ERPs support business processes, information flow, big data analytics, and report generation. The primary software modules found in enterprise systems include supply chain management, manufacturing, projects, financials, human resources, and data warehouse. As one can see from the literature above, it is apparent that manufacturing firms widely recognizes the benefits of ERP and, despite some of the challenges they encounter during implementation, they are widely adopted in the sector. These systems facilitate the information flow within manufacturing firms, hence support strategic decision making. ERPs also eliminate unwarranted cycle times, therefore, improving the efficiency of supply chain management. Noteworthy, optimal benefits of ERP can only be realized with the support of management and a presence of a feasible business plan. Moreover, user involvement, education, as well as training and effective project management contribute the ERPs’ success in manufacturing companies.
Enterprise systems are not intended just for above mentioned firms. In the past decade, ERP vendors have expanded their products to service industries, serve universities, hospitals, and governments among others. Supply chain coordination is an important feature of contemporary and more open enterprise systems. Coordination over ERP-based supply chains proved numerous opportunities for shared benefits. The pitfall is that ERP-linked supply chains call for significant financial investment by their participants to attain compatibility.