Project: Supply Chain Management (SCM)
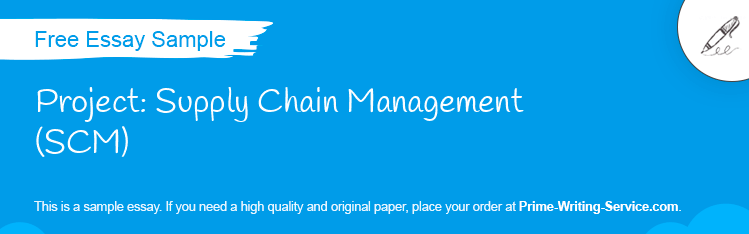
Supply chain management (SCM) is built on a number of principles, the observation of which helps it to perform its functions properly. Elliott (2012) distinguishes seven main principles of SCM:
Therefore, seven mentioned principles of SCM demonstrate that a SC does not consist of separate simple elements, but represents a combination of all processes, which are involved in manufacturing and delivering goods to customers. SCM should follow all seven principles to satisfy the customer needs.
Calculate the cost of essay
Globalization and fast economic development make all companies of different SCs focus on their core competences. Thus, production is concentrated on optimizing manufacturing processes and commercial firms are focused on selling goods with a maximum profit (Hugos, 2011). These ideas made some firms think of whether it is beneficial for them to have their own warehouses and trucks for the goods delivery as the process of transporting the products to the customers is not the core competence of their activities. As a result, nowadays the majority of trucking activities of different companies are outsourced and performed by commercial trucking companies (Hugos, 2011). These companies are called logistics providers for SCs. Transportation is an engine of business competition, which is responsible for the choice of a company made by customers (Hugos, 2011). Trucks are relatively quick and can be sent almost anywhere. Such means of transport is capable of providing a high level of responsiveness for the goods in case of using the services of a reliable logistics provider (Hugos, 2011). The greatest drawback of this means of transport is that it “is prone to fluctuations though, as the cost of fuel fluctuates and the condition of roads varies” (Hugos, 2011, p. 15). All these facts make commercial trucking critical for the effectiveness of any SC and force SC managers to include transportation and logistics planning into their activities as the delivery of goods requires optimization. It is important to calculate the costs of fuel, evaluate the quality of the highways and choose the shortest and safest rout. The method of delivering goods by trucks is closely related to the form of the delivery (direct or indirect). It should be coordinated with the size of a warehouse, which the recipient has. The organization of a truckload shipment is not simple, but the result is worthwhile (Hugos, 2011). Commercial trucking is critical for SCs and is worth special attention as on the one hand, it is very costly for them to keep their own trucks and on the other hand, they will significantly benefit from the transformation outsourcing only if they do some accurate planning (Hugos, 2011).
Limited time offer
Hugos (2011) discusses the importance of transportation planning system in the context of commercial trucking. Before choosing the best logistics provider, a SC manager should determine which quantity of goods should be delivered to a certain destination in a certain period of time. There exist specific software programs to help him/her do it. Hugos (2011) underlines that a company should find all possible ways to deliver its products from one warehouse to different commercial points or customers as this process will greatly reduce the transportation expenses. Commercial trucking is considered to be the most favorable logistical option of the future. The reasons of this fact include the option of using a system of international highways, which is constantly being constructed, and the technological progress (Hugos, 2011). Choosing the mode of transport depends on the aims of the company. Trucks and air transport are more reliable, but costly. Shipping and rail delivery are less expensive, but they usually take more time and are associated with more uncertainty as for the delivery of goods in the same form, in which they have been sent. Therefore, commercial trucking will always stay critical for manufacturing companies, especially those, which compete on the basis of the level of the customer service and convenience and the SCs of which are optimized according to the highest level of responsiveness for the delivered goods. Keeping this idea in mind, it is significant to choose a reliable logistics partner, who will connect all of the elements of a SC and become its integral part.
Benefit from Our Service: Save 25%
Along with the first order offer - 15% discount, you save extra 10% since we provide 300 words/page instead of 275 words/page
An important point of the discussion on SCM is lean thinking or lean business operations, because the main aim of any company is optimization of its activities. The main principles of lean thinking applied to business are as follows: “precisely specify value by specific product, identify the value stream for each product, make value flow without interruptions, let the consumer pull value from the product and pursue perfection” (Hines, n. d., para. 1). It is possible to conclude that the critical point of any lean operation is value and perfection.
Hines (n. d.) states that the value of goods or services can only be defined by an end customer and is meaningful, if it satisfies the customer’s needs. A value stream is a process of continuous designing, engineering and logistics planning and management with the purpose of delivering a valuable product to the customer (Hines, n. d.). “Pulling” can be explained easily: there is no sense for an enterprise to produce anything that the customers do not demand (Hines, n. d.). Finally, when all the principles are observed and the company’s aims are reached, it is time to think about perfecting some manufactured goods (Hines, n. d.).
VIP Services
$2.00Extended revision period
$3.00SMS notification of the order status
$3.66Get order proofread by editor
$4.40Get order prepared by top 30 writers
$5.99Get a full PDF plagiarism report
$9.99Get VIP support
20% OFFVIP services package $23.23
Hines (n. d.) draws the readers’ attention to the fact that the enumerated lean operation principles were originally formulated quite long ago and they do not meet the requirements of modern business and cannot be applied to all industries. The author determines such drawbacks of an original lean system as lack of concentration on resourcing, staff development and training, wider supply chain, poor link with business needs, over focus on order fulfillment, lack of focus on quality and risk prevention and others (Hiner, n.d.). Hiner (n. d.) does not deny the effectiveness of the old lean principles, but offers a modernized system of lean operations to meet the requirements of today’s business. He calls this system “The 8Ps lean thinking”. It includes purpose, process, people, pull, prevention, partnering, planet and perfection (Hiner, n. d.). It is possible to explain each principle in short: (1) before starting an organization, it is needed to exactly define its purpose. All employees should realize what they want to achieve and have a strictly defined range of duties; (2) it is significant to optimize not only one, but all processes. Hines (n. d.) underlines that 95% of the companies with which he worked, applied lean principles to the order fulfillment only and failed to move further; (3) Though all companies try to develop the culture of continuous improvement, it is not enough for being successful. The most important factor in Hines’s (n. d.) opinion is fundamental respect to the workers and the development of leadership abilities among the senior level employees, who will be capable to skillfully manage others; (4) Hines (n. d.) claims that some companies and enterprises do not draw a direct line between the quality improvement and the customer’s demands, though the latter parameter is meant to shape the activities of the company. Organization of pull-based delivery, improvement and training should be the primary goals of any business; (5) the over focus on the trite lean principles regarding tools and techniques may cause some problems, because the usual methods may not be effective. In order to prevent a problem, a company should investigate more innovative tools, which are applicable to a definite situation; (6) The experience of economic scholars and businessmen proves that a SC may function effectively only if all the organizations involved have a close partnership relationship; (7) regardless of the activities performed by a company, there are some common goals in the business world and one of such goals is following the principles of environmental protection; (8) each organization should have its own lean business system to improve the goods or services with the aim of reaching perfection. Therefore, keeping in mind the old principles of lean operation and expanding them following the offered system of 8 components, will make any business effective.
Try our Top 30 Writers
Benefit from the incredible opportunity
at a very reasonable price
Order only for $4.40
Speaking about process selection, it is important to note that this function in the most general sense is assumed by numerous managers, who ensure the effectiveness of a SC. These managers are responsible for the stability of their companies’ SCs, the existence of which is impossible without a set of operations. Each of these operations is very important and forces managers to make more responsible decisions regarding which tactics should be followed. It is possible to consider 4 main groups of SC operations, which are planning, sourcing, making and delivering (Hugos, 2011). Each of these groups comprises of a number of processes, performed by the mentioned managers. Their correct professional selection reflects the needs of a company.
The first two groups of managers, involved in decision-making are senior managers and line managers. Senior managers choose which SC will be organized for a company and line managers supervise its general functioning and discuss the issues with the seniors (Hugos, 2011). A planning stage consists of demand forecasting and pricing planning. Demand forecasting is the basis for any company’s internal operations. It can be performed using four methods: qualitative, casual, time series and simulation. The process selection here depends on the abilities of SC managers and the state of the company. Time series are the most widespread technique as it deals with analyzing the history of demand-supply patterns of the company’s goods. Planning department specialists, as well as store managers as their assistants, perform these functions (Hugos, 2011).
Try our VIP Support
Benefit from the incredible opportunity
at a very reasonable price
Order only for $9.99
The most important choice, which a marketing specialist should make, is “Is it better to do price promotion during peak periods to increase revenue or during low periods to cover costs?” (Hugos, 2011, p. 56). The answer depends on the organization’s cost structure: if a company is flexible in changing the number of employees and the level of productive capacity, the period of the peaks should be chosen; if its flexibility is limited, it is better to choose some lower period. Marketing managers are responsible for this choice (Hugos, 2011).
Procurement function has recently become a complex activity for purchasing managers and consists of 5 main processes: purchasing, consumption management, vendor selection, contract negotiation and contract management (Hugos, 2011). Purchasing department needs help of a planning department, marketing specialists and lawyers to perform all these activities as they supervise the exchange of a great volume of information and contract signing (Hugos, 2011). The sourcing operations are represented by credit and collection activities, when a company’s aim is to receive money planned for the goods. A good credit manager “tries to fulfill customer demand for products and also minimize the amount of money tied up in receivables” (Hugos, 2011, p. 70). The general credit policy is determined by the senior managers of a company (Hugos, 2011). It is very useful for a company to have a risk manager to manage credit risks. Product design and scheduling, which are the stages of making operations, are performed by designers, brand managers and a planning department, which calculates and correlates the capacity of the company and its delivery (Hugos, 2011). The last stage of delivering is order management. The complete information about the order is transferred through the entire SC. Marketing and transportation managers are the leading professionals to perform these activities. Therefore, the described model of a company, which is represented by different managers with a determined set of responsibilities, is an ideal option for normal functioning of a company. If the senior managers want to ensure that their SC functions in a stable way, they should hire the maximum amount of managers and distribute responsibilities among them.